Monitoring My Favorite Kitchen Appliance
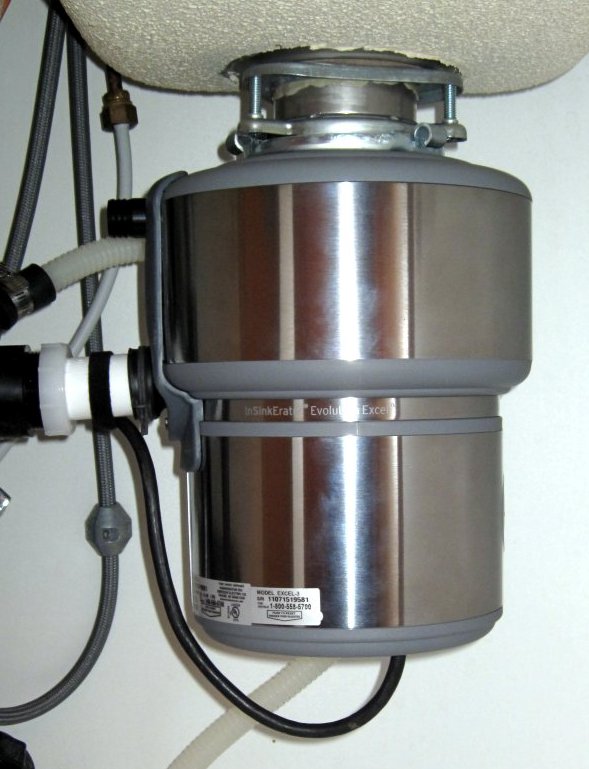
Instant gratification is rarely a good thing. The virtue of patience is not learned in an instant, but after repeatedly enduring opportunities to be patient while maintaining both one’s temper in the face of trying circumstances and a healthy perspective. Patience can work together with anticipation, and over time they spice up the reward long desired. Not quite the paragraph you expected to read beneath the header, above, is it? Let me esplain… No there is too much. Let me sum up:
When I got married to my wonderful wife, I found all sorts of new things in the sink: Orange peels, potato peels, onion peels, banana peels, all manner of fruit and vegetable stems, husks, shells and skins. I quickly found that when I did not know what to do, I should clean something, and so it became my task to clean the kitchen after most supper meals. I would spend considerable time manually grinding up these things into bits and pieces small enough to squeeze through the straining bars at the bottom of the sink. In fact, I would often grind in a circular motion, pretending myself to be a garburator.
All those nights spent grinding up the leftovers from dinner’s preparation had me longing to install a real garburator. I’d been to friends’ houses who had them and loved the simple cleanup they offered. Growing up in an Irish household, I cannot begin to imagine the truckloads of potatoes my dear mother must have peeled over the years. All those potato skins were bagged up, tossed out with the trash and sent to landfills. While biodegradable, they certainly added to the bulk of waste produced by our household. As well, it is the organics in the trash that cause the most stink. Some day, I thought to myself, I will get a garburator!
After at least a year or yearning, an opportunity presented itself to purchase one – in fact, quite a high quality “In-Sinkerator” brand food waste disposer. Although I had never done so in the past, I managed to install the unit in under three hours, and it was only a two-trip installation. (A lot of times I rate my installations in terms of trips – that is, how many trips I have to make to Home Depot before I had all the correct parts, tools and accessories.) The model we got had a full 1 HP motor and various design features to make it extra quiet while pulverizing whatever you placed down it’s throat. From that very first test until this very night, I have continued to challenge the unit with materials that I would never consider stuffing down a 3″ drain pipe. Invariably, it has reduced them all to crumb-sized bits and washed them down the drain with ease! All manner of peels and rinds, avocado pits don’t even make a bump. Un-popped popcorn, masses of potato peels, whole chicken and turkey carcasses go through bone like butter, all without the mess or stench of a pig farm. Without a doubt, it is my favourite kitchen appliance.
Electrically, it’s grinding force draws a lot of power, and one afternoon I was contemplating how I might be better able to ascertain how I spend money on electricity. I already monitor the current drawn through both electrical phases entering the house, and short of adding current sensors on every branch circuit I thought there might be better ways of figuring out what some of the peaks in the amperage graphs originate from. I started designing in my head a device that could be embedded into the electrical system of any household appliance, big or small, that would monitor even multiple devices within that appliance and report on their usage patterns. Take a refrigerator for example: We all know that refrigerators have a compressor, fans and light bulbs that turn on when you open the door. But most people would be surprised to learn that they also have electric heaters in them! Yes – the appliance that keeps your milk cold and your steaks frozen does so with the help of electric heaters! If I had a device that I could tie into the electrical system of the refrigerator to monitor when each of these components was used, I’d get a very interesting graph of how the appliance works; perhaps even some ideas on how to save electricity.
One of the first challenges with this idea is that micro-controllers run on 5 volts DC or less, while the fans, motors and heaters in the fridge run on 120 volts AC: nary the two should meet! Traditionally, to monitor AC power presence with a micro-controller, one could install a 120V relay and then connect an input pin through one of the Normally Open sets of contacts. When mains voltage was applied to the coil of the relay it would pull the contacts closed, make the Normally Open circuit and signal the micro-controller. While this does ensure electrical separation between the mains power and the micro-controller circuitry, this method has some drawbacks: 1. Cost. A typical 120VAC relay could run between $10 and $50, usually depending on the type of load switched. Since we are really only switching a signalling load, the smallest relay we can find would suffice. There is also noise: relays make a click when they activate and de-activate, and if the appliance turns components on and off frequently, the clicking noise produced by the relay may not pass the acoustic department of the aesthetics committee.
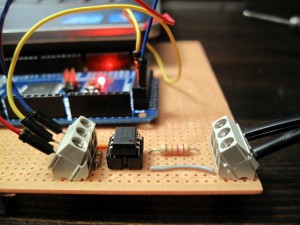
I started doing some research on ways to detect AC presence. There was a number of technologies that looked interesting, however I came across one component designed specifically for the task: The MID400. Basically comprised of a pair of LED’s aimed at a photo-sensor connected to a “slow” op-amp, the MID400 does exactly what I need it to. Connect the LED pair to the mains voltage with a suitable resistor for current limitation and each LED shines on the photo-sensor during it’s corresponding cycle of the alternating current waveform. The “slow” op-amp allows the output to remain low even during the zero-crossing when both LED’s would be off, but removal of power causes the op-amp to send the output high after about 50 ms if I remember correctly. See the picture above for my prototype; that is 120V AC connected to the terminal block at the right, and the three pins on the left are connected to my Arduino Mega, seen in the background. It was a suspenseful moment as I first connected the mains power to this small circuit. Let me just say that I checked the pins of the MID400 four or five times first! However, there was no smoke or loud bangs – in fact, the whole thing worked exactly as it was supposed to. There is no noise, these parts are cheaper than AC-driven relays, and small! The ones I bought to sample are an 8-pin DIP configuration. Later on, I added an [external] LED for visual confirmation when AC is sensed, and set one of these up to monitor when the In-Sinkerator is running. The output is sent back to a VDAC (Venturii Data Acquisition and Control) board, and monitored by Venturii.
It’s been running for several months now, and I’m hoping to get a test run of manufactured circuit boards made by Metal Minds in the next few weeks to replace my hack-job prototype. If the next prototype works well, we may begin to sell these as an AC presence sensor that could be used to detect whenever any AC appliance or device is on or off with any TTL-compatible input. The board takes 5VDC in, and the output pin goes high (+5V) whenever AC is absent (off) and low (GND) whenever the AC is detected (on.) The LED also reflects the AC presence, so long as there is 5v power to the board. Somewhere I have a picture of the revised prototype that is currently under my sink. The InSinkerator plug beneath the kitchen sink has two receptacles, so I have the InSinkerator plugged into one and my AC Presence Sensor plugged into the other; whenever the InSinkerator switch is turned on, it also sends power to to the AC Presence Sensor, which signals a VDAC board and this gets logged within Venturii. Optionally, I could have Venturii do something else when this input changes state – I just don’t know what would be useful.
This proof of concept will hopefully pave the way for a new board I am working on in my head, to embed some more monitoring and/or manual, semi-automatic, or fully automatic control of the inner workings of other appliances. One in particular that comes to mind is the fridge, and I believe I have touched on this idea in another post – possibly on the Venturii Vacuum Cleaner. By incorporating a temperature sensor into the refrigeration and freezer compartments, and replacing the inner workings (usually mechanical timers, etc.) with a smart control board, it may be possible to reduce energy costs based on both internal intelligence (better motor, heater, and fan control directly related to temperatures of various components; even ambient air temperature) as well as external influences such as whether or not anyone is in the house, what time of day it is, what day of week it is, and how likely it is that someone is going to open either part at that time. It seems, based on my power consumption graphs, that the heater is governed not by any sort of sensor but by a mechanical timer that simply turns it on at a regular interval, whether or not the condenser coil is freezing up or not. This heater draws several amps – I’m pretty sure it’s as much as or more than the compressor motor and fans combined! If it didn’t need to run as much, electrical consumption would be reduced. Imagine also, the fridge ramping up the compressor runtime around breakfast, lunch, and dinner in anticipation of the door being opened more frequently, better compensating for heat gained every time it is opened.
There are so many ways appliances could be improved, by adding a little smarts to the way they operate. Of course, the flip side is that introducing new technology to replace a proven, albeit sub-optimal, control system adds a greater risk of malfunction. Suppose the new controller did not turn the compressor on when it should and all the food within the fridge warmed to room temperature before anyone noticed. What I need is a bar fridge or an old full sized fridge to tinker with as I develop and perfect these innovative technologies. Does anyone have an old fridge they’d like to part with for a good cause?